Table of Contents
** Minutes
Why accurate net & gross weight measurement is crucial in ecommerce
Optimize your shipping and inventory with ShipBob’s precision tools
For ecommerce businesses that are shipping physical products, every ounce matters—literally. The difference between net weight and gross weight can impact your entire operation, affecting shipping costs, customer experience, and inventory management. Get it wrong, and you could be paying more than you should. Get it right, and it can greatly improve your bottom line.
In this guide, we’ll unpack what net weight and gross weight are, why they matter, how to ship a package efficiently with precise weight calculations, and how ShipBob can help keep things running smoothly.
What is net weight?
Net weight refers to the actual weight of the product itself, without any packaging or additional materials. For instance, if you sell jars of honey, the net weight is the honey inside the jar, excluding the jar, lid, or labels.
Net weight is essential for transparency, especially in industries like food or cosmetics, where customers expect—and regulations may require—clear product weight information.
How does net weight apply to shipping?
For ecommerce businesses, understanding net weight can provide several key benefits.
Inventory management
Net weight is essential for accurate stock tracking. By knowing the precise weight of a product, you can verify shipments, spot discrepancies, and streamline audits. For example, if your system shows 100 jars of honey but the total weight doesn’t align with the net weight per jar, it’s a clear sign something’s off. This is especially valuable when working with systems like ShipBob’s warehouse management system (WMS), where maintaining accurate records ensures smooth operations.
Regulatory compliance
Many industries are legally required to list net weight on their product labels. For example, selling bags of coffee or boxes of tea in the U.S. requires clear, accurate net weight labeling. Mislabeling can result in fines or penalties.
Shipping cost calculations
Knowing net weight, total gross weight, and dimensional weight gives you a complete picture of your shipping costs. This helps ensure you’re not unknowingly overpaying due to unnecessary packaging or miscalculated billable weight.
How to calculate net weight
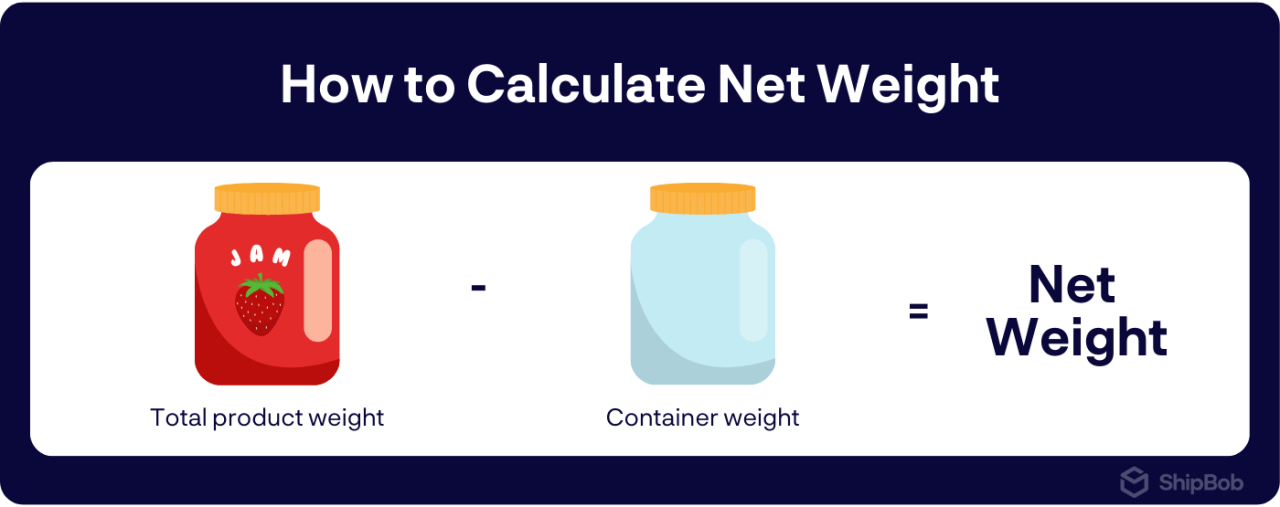
To calculate net weight, begin by subtracting the weight of the packaging materials from the total weight. Here are some practical examples:
Example 1: Selling jars of jam
- Total weight of the jar and the jar’s contents: 2.78 lbs
- Weight of the empty jar: 2 lbs
Net weight = 2.78 lbs (total) – 2 lbs (jar) = .78 lbs or 12.48 oz
Example 2: T-shirts in poly bags
- Total weight of the packed t-shirt: 0.6 lbs
- Weight of the poly bag: 0.1 lbs
Net weight = 0.6 lbs – 0.1 lbs = 0.5 lbs
What is gross weight?
Gross weight is the total weight of the product, including all dunnage and packaging materials, shipping boxes, protective fillers, and other contents. This is the weight that shipping companies use to determine shipping fees.
How does gross weight apply to shipping?
Gross weight is a critical metric in the shipping process, as it directly impacts a few key aspects of your operations.
Shipping fees
Carriers calculate fees using either gross weight or dimensional weight, depending on which is greater. Knowing the gross weight of a shipment helps ensure you’re not blindsided by unexpected charges.
Packaging optimization
Businesses can reduce material costs and shipping fees by balancing the weight of the goods with appropriate packaging. For instance, oversized or heavy packaging can inflate gross weight unnecessarily.
Customer satisfaction
Bulky or excessively heavy packaging can leave customers feeling annoyed, especially if it seems wasteful or difficult to handle. Thoughtfully designed, efficient packaging ensures products arrive safely without unnecessary weight, keeping shipping costs reasonable and leaving customers with a positive impression.
How to calculate gross weight

To determine gross weight, add the product’s net weight to the weight of all packaging materials. In terms of bulk shipments, packaging materials could include pallets, boxes, crates, etc. Whereas for smaller shipments, it might include items like shipping boxes, bubble wrap, and protective inserts.
Here are some examples:
Example 1: Shipping a smartphone
- Net weight of the phone: 0.4 lbs
- Weight of the retail box, charger, and user manual: 1 lbs
- Weight of the shipping box and protective bubble wrap: 0.6 lbs
Gross weight = 0.4 lbs (phone) + 1 lbs (retail box, charger, and manual) + 0.6 lbs (shipping materials) = 2 lbs
Example 2: Bulk shipment of furniture
- Net weight of the goods: 1,000 lbs (total weight of all furniture pieces without packaging)
- Weight of the wooden crate: 200 lbs (used to enclose and protect the furniture)
- Weight of the pallet: 50 lbs
- Weight of straps and dunnage: 25 lbs (to secure the furniture during transit)
Gross weight = 1,000 lbs (furniture) + 200 lbs (crate) + 50 lbs (pallet) + 25 lbs (straps and dunnage) = 1,275 lbs
Why accurate net & gross weight measurement is crucial in ecommerce
Getting net and gross weight measurements right isn’t just about crunching numbers—it’s about making your entire ecommerce fulfillment operations smoother.
Significant impact on shipping costs
Shippers base fees on billable weight, the greater of gross or dimensional weight, making accurate weight data essential to avoid unnecessary costs. Overestimating weight in your shipping documents (e.g. bill of lading) can inflate the cost of shipping goods more than necessary, while underestimating can result in carrier adjustments and unexpected fees.
Regulatory compliance
Industries like food, cosmetics, and pharmaceuticals are heavily regulated when it comes to labeling. Net weight must be accurate and compliant with industry standards, or you risk penalties, fines, or even product recalls. A food business overstating its net weight on a product label could face legal repercussions, not to mention a loss of trust from customers.
Operational efficiency
Accurate weight data streamlines processes from start to finish. With precise measurements, businesses can automate workflows like picking, packing, and shipping with the help of 3PL companies like ShipBob.
Satisfying customer expectations
Customers expect what they see on the product page to match what they receive. Accurate weight measurements ensure customers aren’t misled about what they’re buying. Plus, optimized packaging contributes to a better unboxing experience.
Avoiding discrepancies and returns
Incorrect weight data can create downstream problems, like shipping delays, extra costs, or returns. For instance, if a customer orders a 10-lb dumbbell and receives one that weighs 8 lbs due to miscalculated net weight, they’re likely to feel deceived and request a return.
International shipping considerations
For businesses shipping globally, accurate weight calculations are even more crucial. Many countries enforce strict weight regulations, and incorrect gross or net weight declarations can result in delays or penalties. Additionally, understanding the mode of transportation used (air, sea, or land) can affect how carriers evaluate the weight of the cargo for pricing.
Optimize your shipping and inventory with ShipBob’s precision tools
ShipBob offers a suite of advanced tools and systems to help ecommerce businesses manage net and gross weight effectively. As a trusted fulfillment provider, ShipBob streamlines operations, cuts unnecessary costs, and enhances the end customer’s experience.
Advanced shipping calculations
ShipBob integrates with digital weighing scales to automatically capture and record weights, ensuring accuracy and reducing both manual errors and ecommerce shipping costs. This ensures you can confidently offer competitive shipping rates without overpaying. Whether you’re shipping lightweight accessories or heavy goods, ShipBob ensures that every package is optimized for cost-effectiveness.
Inventory management

ShipBob’s WMS helps streamline inventory management by providing accurate data and tools to reduce discrepancies. For example, if a shipment’s weight doesn’t align with expectations during an audit, it can signal an issue that needs investigation. These insights ensure smoother operations, more reliable stock tracking, and improved reordering efficiency.
Custom packaging solutions
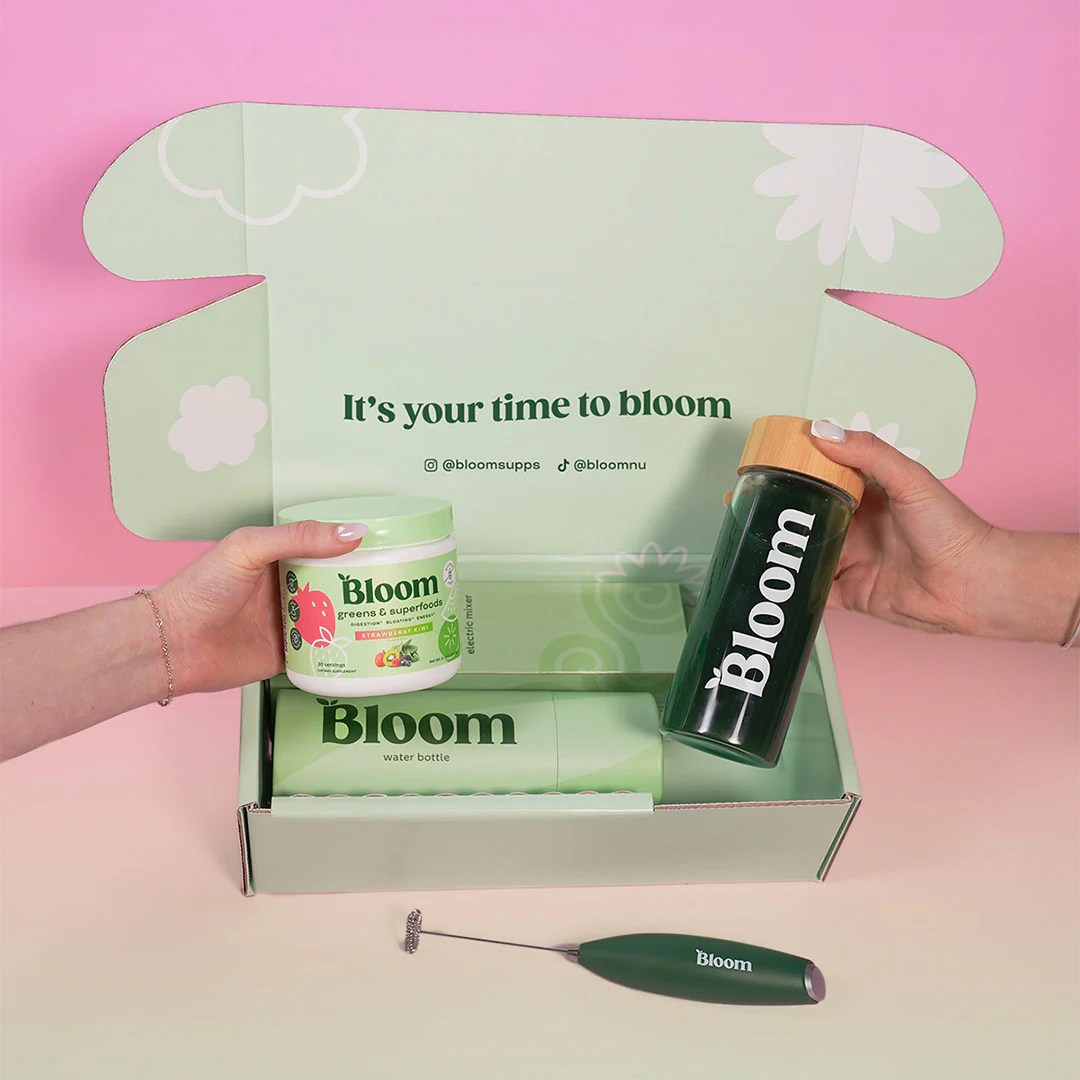
Packaging isn’t just about protecting your products—it’s about balancing customization, costs, and sustainability. ShipBob works with businesses to create packaging solutions that minimize unnecessary weight while ensuring items arrive intact. This not only helps you reduce shipping costs but also appeals to eco-conscious customers who value sustainable practices.
Automated order fulfillment
Accurate weight data powers automation in ShipBob’s fulfillment centers. From using a box selection algorithm for finding the right-sized box to calculating shipping costs, ShipBob uses precise measurements to streamline the packing and shipping process.
Case studies and success stories
By managing net and gross weight data, ShipBob helps brands streamline operations, cut costs, and deliver a better customer experience. Let’s take a look at how two businesses have used ShipBob to achieve impressive results.
Our Place
Our Place, a cookware and home goods brand, partnered with ShipBob to achieve greater transparency in shipping costs and weight tracking. Previously, they struggled with their 3PL partner’s outdated billing practices, which made it hard to verify the gross weight of a shipment.
With ShipBob’s technology, Our Place gained clear visibility into actual weight, dimensions, and carrier fees. This allowed them to ensure accurate billing, eliminate frequent disputes, and streamline their shipping processes with data-driven insights.
“I couldn’t fathom reverting to our previous billing practices with prior 3PL partners. We would receive Excel spreadsheets and struggle to verify if the dimensions and weights of our shipped parcels were accurate. We had to rely solely on the word of our old 3PL. Determining whether a carrier had added a particular accessorial charge was challenging, and often, the charges seemed unjustified. Nearly every month, we found ourselves having to request credits due to discrepancies.
After transitioning to ShipBob, I receive a consolidated bill encompassing all picking, packing, and outbound freight charges. There’s no ambiguity regarding the bill’s accuracy.”
Ali Shahid, COO of Our Place
ZBiotics
ZBiotics, a health and wellness brand, teamed up with ShipBob to tweak their packaging and cut down on shipping costs. They wanted to make sure their shipments stayed within specific weight bands that carriers use to calculate fees.
ShipBob’s team reviewed the shipment’s dimensions and weight, noting the initial packaging design exceeded dimensional weight thresholds and wouldn’t save costs. With their feedback, ZBiotics redesigned a smaller box that reduced shipping costs and complied with weight regulations.
“We redesigned our secondary packaging (product boxes), reducing costs by source reduction (using less material), domestic manufacturing (lower freight), and greatly reduced lead times (for better cash flow).
Our Merchant Success Manager at ShipBob was helpful through this process. When we were deciding on new packaging, the ShipBob team would analyze dimensions to ensure we were staying under a certain weight band.”
Michael Mullaney, VP of Supply Chain at ZBiotics
Get started with ShipBob
Want to learn more about ShipBob’s fulfillment solution? Connect with our team for a customized quote.
Net weight vs. Gross weight FAQs
What is TARE weight?
TARE weight is the weight of the empty container or packaging that holds the goods, without the product inside.
What’s the difference between net, TARE, and gross weight?
- Net weight: Product weight
- TARE weight: Packaging weight
- Gross weight: Net weight + TARE weight
What is an example of net weight?
Net weight is the weight of the product itself, excluding packaging and other materials. For example, if a bottle of shampoo weighs 1.2 lbs with the bottle, and the bottle alone weighs 0.3 lbs, the net weight of the shampoo is 0.9 lbs.
Why is understanding net and gross weight important for shipping?
Understanding net and gross weight is essential for accurate shipping fees, compliance with regulations, and efficient inventory management. Net weight ensures proper labeling and inventory tracking, while gross weight is critical for calculating shipping costs and designing efficient packaging.
How does ShipBob ensure accurate weight management?
ShipBob provides tools and technology designed to help businesses manage weights throughout the shipping process. This helps businesses optimize shipping costs by ensuring weights are correctly recorded, minimizing errors, and aligning with carrier pricing models for the best possible rates.