Table of Contents
** Minutes
Key warehouse report types every business needs
How reporting improves warehouse performance
How to get started with warehouse reporting
Running a warehouse without clear reports can be full of guesswork. These reports give you the tools to monitor inventory levels, track order accuracy, and identify inefficiencies before they become major issues.
With the right systems in place, like a powerful warehouse management system (WMS), you can automate these reports and get real-time insights into every corner of your operation. In this guide, we’ll break down the importance of warehouse reporting and how it can help you streamline your operations, reduce costs, and stay ahead of bottlenecks.
What is warehouse reporting?
Warehouse reporting involves gathering and analyzing data to get a clear picture of your entire warehouse operations. From tracking which products are moving quickly to identifying where workflows are slowing down, these reports provide clarity in an often chaotic environment.
For example, inventory reports might show that your best-selling items are running low, prompting quick reordering, while operational reports could reveal inefficiencies in the packing process.
Warehouse reports unlock data-driven decision-making
Companies that prioritize warehouse reporting can identify trends, improve productivity, and adapt to changes in demand. For instance, reports tracking inventory movement and order fulfillment rates help supply chain managers anticipate bottlenecks before they escalate, ensuring smoother operations.
On the flip side, businesses that neglect warehouse reporting often find themselves stuck in reactive mode—scrambling to fix issues like delayed shipments, inventory shortages, or misallocated resources.
Key warehouse report types every business needs
There are tons of warehouse report types a business can look at to try and identify areas for improvement. However, there are a few key reports every business should consider to get the most value out of their data.
Inventory reports
Inventory reports track stock levels, turnover rates, and reorder points so you can keep everything in balance. By monitoring stock flow, you can avoid overstocking and ensure your top products are always ready to ship.
Order fulfillment reports
If customers are complaining about late deliveries or incorrect orders, order fulfillment reports can help. These reports track key metrics like:
- Order accuracy: Tracks how often orders are fulfilled correctly—reducing returns and customer complaints. Low accuracy may indicate training gaps, unclear processes, or an inefficient warehouse layout.
- Shipping performance: Measures how well delivery timelines are met, helping identify delays caused by internal processes or external carriers. Improving this ensures faster, more reliable shipping.
- Processing times: Focuses on the time it takes to move an order through the fulfillment process—from order placement to shipment.
Operational efficiency metrics
Think of these as the scorecards for your warehouse team. These reports measure things like picking/packing speed and employee productivity. Use them to identify productivity gaps and find ways to work smarter. Metrics like warehouse KPIs are especially helpful in keeping your team on track.
Customer satisfaction metrics
Customer satisfaction drives loyalty and long-term growth, making it critical to track key metrics like delivery times and order accuracy. These metrics reveal how well your fulfillment process meets expectations and where improvements are needed.
Additionally, tracking the repeat purchase rate provides insight into how often customers return, a clear sign of satisfaction with their overall experience. Tools like Net Promoter Score (NPS) or customer feedback surveys can offer further details on what’s working and what’s not.
How reporting improves warehouse performance
Having access to the proper reports gives business owners the insights they need to improve operational performance. Analyzing and acting upon the data in a report can help in cutting costs, optimizing capital allocation, and improving overall efficiency.
Identify bottlenecks and inefficiencies
From misplaced inventory to slow order picking, warehouse reports shine a light on where things are going wrong. For example, order fulfillment reports can highlight delays in shipping times, revealing bottlenecks in the picking or packing process. Similarly, operational efficiency metrics might uncover areas where productivity is lagging, such as certain workstations or tasks taking longer than expected, indicating a need for process improvements or additional training.
Optimize inventory placement and turnover
Warehouse reports paired with dynamic storage strategies help business owners figure out the best spots for high-demand items and ensure slow-moving inventory doesn’t take up valuable space. With the right strategy, you’ll reduce costs and speed up order fulfillment while maximizing warehouse capacity.
“ShipBob’s analytics dashboard has a lot of valuable reports that show our top-selling states, order revenue and costs, units sold, sales by SKU, days of inventory, SKU velocity, sales vs. inventory distributions showing where our customers are and where we’re shipping from, and more.”
Andrew Hardy, COO of Nature’s Ultra
Enhance forecasting and planning
Want to know what your customers will want next month? Reports that show sales trends and inventory turnover can help you plan ahead, avoid stockouts, and keep your customers happy. Businesses that leverage smart warehousing are particularly well-equipped to use this data for better forecasting.

How to get started with warehouse reporting
Setting up effective warehouse reporting may seem daunting, but it’s easier than you think. With the right steps and tools, you can start collecting valuable data and turning it into actionable insights.
Establish KPIs for warehousing operations
To measure performance, you need the right benchmarks. Focus on KPIs such as:
- Order accuracy rate
- Inventory turnover ratio
- Average delivery time
These metrics provide a clear picture of how well your warehouse is functioning. Set targets for improvement and regularly track your progress to ensure you’re meeting your goals.
Analyze thoroughly and optimize regularly
Having reports is just the first step—what you do with the data is what matters. Set a routine to review your warehouse reports, identify trends, and act on insights. For example, if your reports show rising order processing times, investigate potential causes like inventory misplacement or inefficiencies in your workflow.
Automate insightful reports with a WMS
Manually managing data can be time-consuming and prone to errors. A WMS simplifies everything by automating reports, providing real-time tracking of inventory and orders, and offering actionable insights. Tools like ShipBob’s inventory management software eliminate the need for spreadsheets, allowing you to focus on making data-driven decisions that improve your warehouse operations.
“I used to have to pull inventory numbers from three places everyday and move all the disparate data into a spreadsheet. ShipBob has an analytics tab in their dashboard with all of this information, which is great for end-of-month reconciliations.”
Wes Brown, Head of Operations at Black Claw LLC
Elevate your warehousing management with ShipBob’s WMS
Effective warehouse management starts with having the right tools to track, analyze, and optimize operations. ShipBob’s WMS is designed to give you complete control over your warehouse, from real-time tracking to detailed analytics, all in one user-friendly platform. Whether you’re aiming to improve warehouse reporting, streamline processes, or scale your business, ShipBob’s WMS can take your operations to the next level.
Real-time warehouse management software
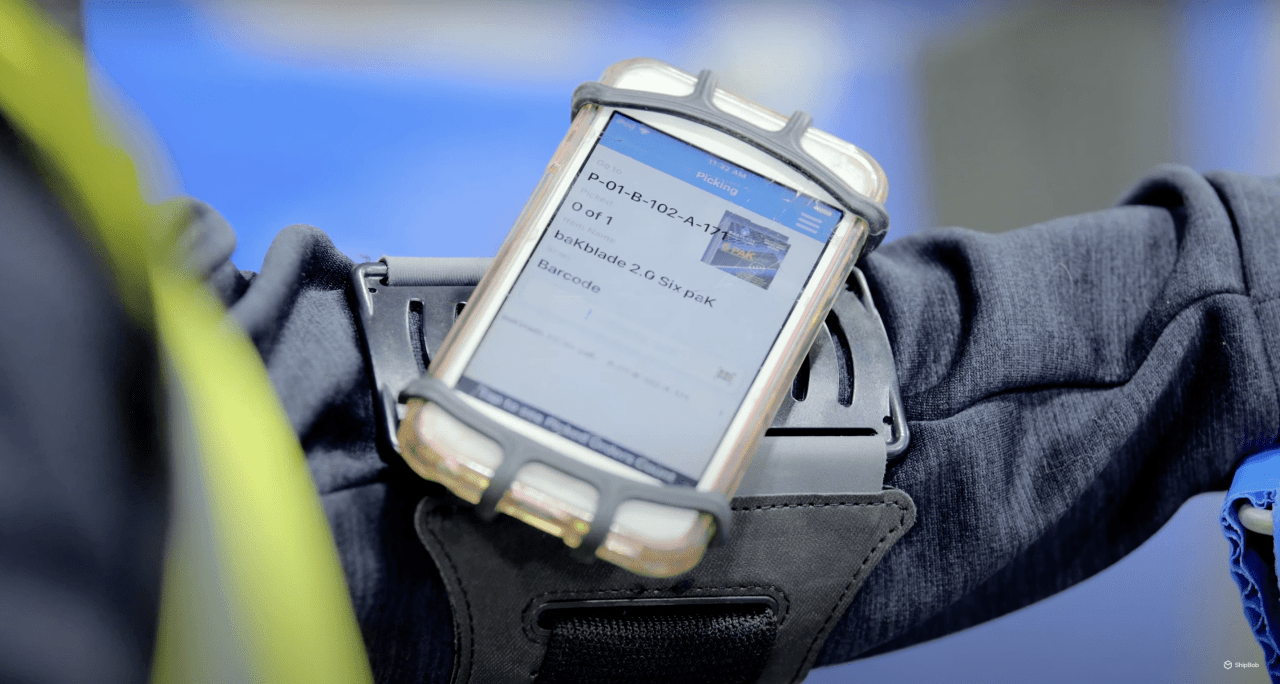
ShipBob’s WMS empowers businesses to manage their ecommerce warehousing needs with precision. With real-time tracking of inventory, orders, and fulfillment, you’ll always know what’s happening across your operations. For example, you can monitor stock levels as they change, track the progress of orders from picking to shipping, and instantly identify inefficiencies like misplaced inventory or delayed shipments.
Comprehensive dashboard and real-time analytics
Say goodbye to guesswork—ShipBob’s WMS provides a centralized dashboard packed with actionable insights. Track key metrics like shipping costs, transit times, inventory levels, and order fulfillment rates, all in one place.
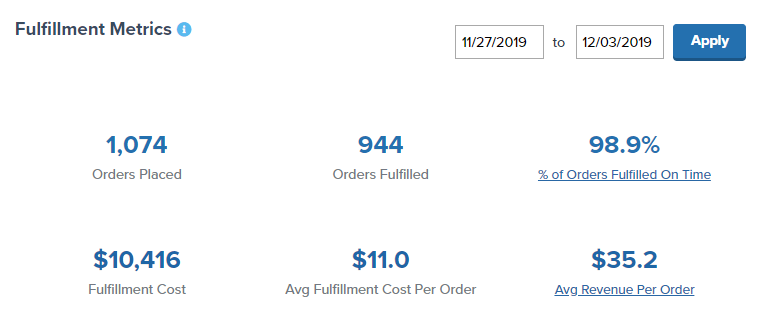
These reports allow you to identify trends, make informed decisions, and optimize your warehouse operations.
Seamless integration and scalability

As your business grows, ShipBob’s WMS grows with you. The system integrates seamlessly with popular ecommerce platforms like Shopify, BigCommerce, and WooCommerce, syncing your orders and inventory with ease. Whether you’re managing a single warehouse, expanding to multiple locations, or leveraging on-demand warehousing for peak seasons, ShipBob’s WMS adapts to your needs, ensuring your operations remain smooth and scalable.
Get started with ShipBob
Leverage ShipBob’s fulfillment technology in your warehouse. Request a quote to learn more about our WMS and get started.
Warehouse reporting FAQs
How can warehouse reports reduce costs?
Warehouse reports help cut costs by identifying inefficiencies, optimizing inventory placement, and preventing overstocking or stockouts. This allows you to allocate resources effectively and avoid unnecessary expenses.
What tools are best for warehouse reporting?
A WMS is ideal for automated reporting. It tracks inventory, order accuracy, and fulfillment performance in real-time, reducing manual errors and saving time.
How can real-time warehouse reporting improve inventory management?
Real-time reporting provides instant visibility into stock levels, helping you avoid stockouts and overstocking. This ensures your most popular items are always available and keeps inventory balanced.
How can ShipBob help with warehouse reporting?
ShipBob’s WMS offers real-time tracking, automated reporting, and actionable insights to streamline your warehouse operations. It’s designed to help you make smarter decisions and scale your business efficiently.